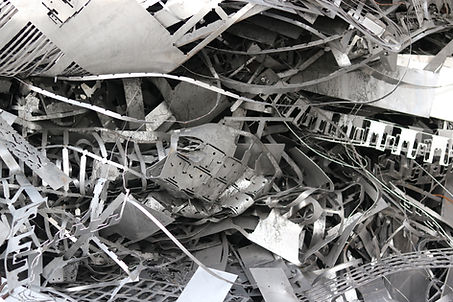
STORIA
La nostra Società, situata 15 km a nord di Milano, venne fondata nel 1926 da Luigi Premoli, per il trattamento di rottami metallici e la loro raffinazione in leghe titolate.
A quasi un secolo dalla sua fondazione, l'Azienda si colloca quindi tra le più longeve della metallurgia italiana.
L'attività si concentrò inizialmente sul recupero di leghe di rame e di zinco, metalli più comunemente impiegati a quel tempo tra i non ferrosi.
Solo con l'avvento della Seconda Guerra Mondiale, l'alluminio, la cui raffinazione elettrolitica solo da pochissimi decenni era stata messa a punto, uscì dalla sua originaria posizione di metallo pressoché raro, per assurgere al ruolo di maggior alternativa all'acciaio, tra i materiali da costruzione.
Intuendone la grande potenzialità, il fondatore, ormai coadiuvato dai tre figli, decise di focalizzare l'attività aziendale proprio su questo promettente metallo.
Il nuovo stabilimento, sorto nel 1946, venne perciò interamente dedicato al trattamento e alla fusione di alluminio.
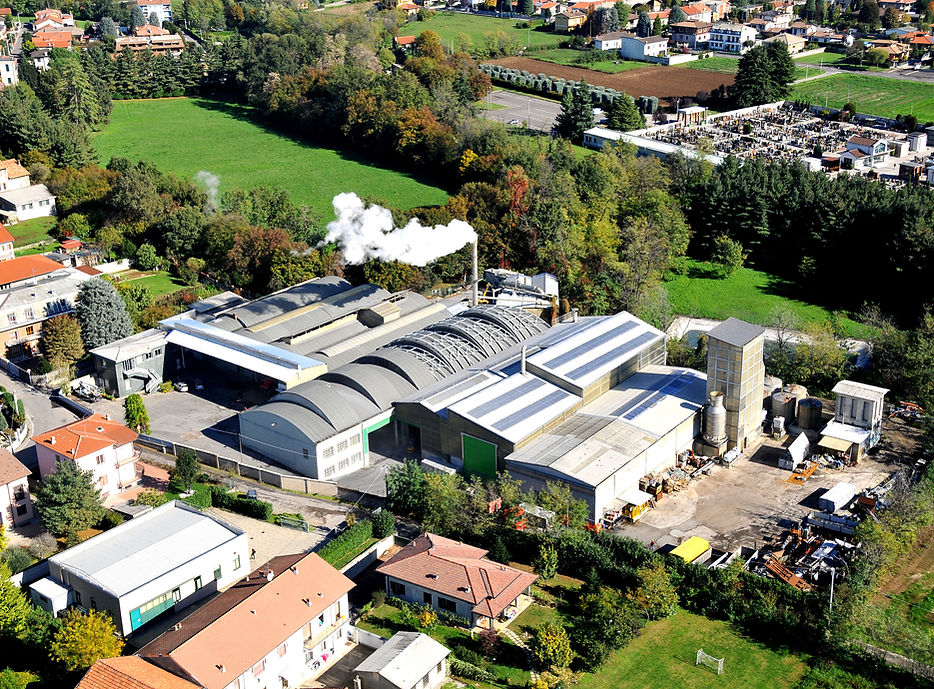
Negli Anni Sessanta, con largo anticipo sulla concorrenza, il primo impianto per l'atomizzazione di alluminio fuso, mediante iniezione con aria compressa ad alta pressione, venne da noi installato nel medesimo sito. Prese avvio quindi la produzione di polveri e granuli metallici, prevalentemente destinati all'industria chimica, estrattiva (esplosivi) e siderurgica.
Negli Anni Settanta, l'acquisizione di una vasta area industriale (150.000 mq ca.) permise la costruzione di una seconda unità produttiva.
L'edificazione di oltre 25.000 mq di capannoni industriali, consentì di minimizzare l'impatto dell'attività, grazie al completo confinamento non solo degli impianti, ma anche di tutte le scorte di materie prime e di prodotti.

Al fine di poter trattare nel modo più idoneo le varie tipologie di materiali disponibili sul mercato, garantendo nel contempo il rispetto degli standard ambientali, vennero installati una pluralità di impianti dedicati. Particolare attenzione venne prestata alla progettazione e realizzazione in proprio di sistemi di cesoiatura e macinazione per la riduzione dimensionale delle materie prime, presupposto indispensabile alla successiva fase di selezione/concentrazione della carica, destinata alla fusione.
Nel corso degli Anni Ottanta, l'esperienza acquisita nel trattamento dei residui di fusione dell'Alluminio (schiumature, scorie, ecc.) ed ulteriori sperimentazioni dirette nel campo idrometallurgico, consentirono di sviluppare un processo specifico per il completo recupero di tutti i singoli componenti di tali residui.
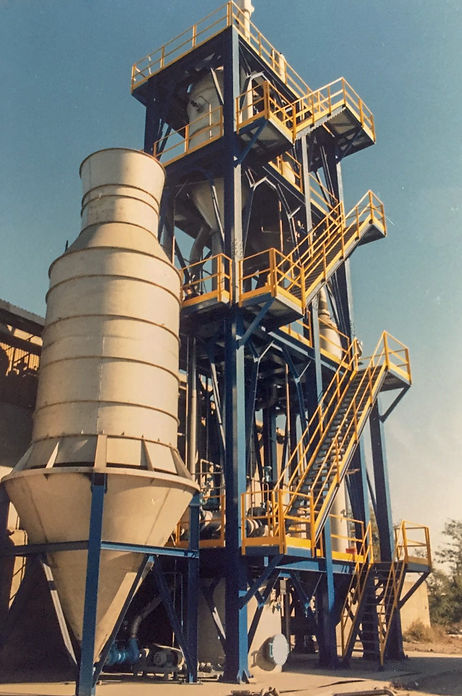_edited.jpg)
Questo processo divenne ben presto il parametro di riferimento per tutti gli operatori del settore e, nonostante il lungo periodo ormai trascorso, esso è tuttora indicato come BAT ("Best Available Technique") anche nella recente revisione delle linee guida comunitarie per l'attività di raffinazione di alluminio.
Il processo prevede il lavaggio completo dei residui, provocando la dissoluzione dei sali contenuti. La salamoia risultante viene ricircolata fino alla saturazione, mentre le parti insolubili (prevalentemente ossidi di alluminio), vengono separati ed essiccati, prima dell'invio al recupero.
Un apposito impianto di evaporazione d'acqua, consente la cristallizzazione dei sali contenuti nella salamoia, mentre l'acqua evaporata viene ricondensata per essere nuovamente impiegato a ciclo chiuso nel sistema.
Grazie a questo processo, per la prima volta al mondo l'annoso irrisolto problema, connesso ai residui provenienti dalla fusione di alluminio, trovò finalmente una soluzione percorribile dal punto di vista industriale ed ambientale.
Il conseguimento di tale traguardo consentì all'azienda sin dal 1987 (oltre un decennio in anticipo sulla concorrenza) l'ottenimento di specifica autorizzazione per il recupero (fino a 100 t/giorno) di tutte le tipologie di scarti e residui di alluminio (rottami, torniture, schiumature, scorie, polveri, ecc.), anche qualora classificati come "Rifiuti Pericolosi".
I suddetti rifiuti sono accuratamente selezionati ed opportunamente condizionati nel nostro processo di trattamento, in modo da rispettare le specifiche richieste di utilizzatori a valle, che li possono così positivamente reimpiegare come materie seconde per usi industriali.
Nessuna frazione viene smaltita, ma il 100% dei componenti trovano riutilizzo industriale, antesignano esempio di "Circular Economy".
La piena rispondenza anche ai requisiti tecnico-professionali, dettati dai nuovi standard europei, ha permesso alla nostra Società il tempestivo conseguimento (2006) anche della Autorizzazione Integrata Ambientale (A.I.A.), che costituisce il nuovo strumento autorizzatorio per la corretta gestione e trattamento dei rottami/rifiuti metallici.
Non di minore entità è stato negli ultimi 40 anni l'impegno da noi profuso per ampliare ed ammodernare la capacità produttiva di leghe: due nuove linee di fusione e alligazione, assistite da impilamento e confezionamento automatico, hanno permesso di raggiungere una potenzialità di circa 20.000 t/anno di produzione.
Il rispetto delle sempre più stringenti normative ambientali è assicurato da un sistema di filtrazione fumi di ultima generazione, recentemente potenziato ed innovato.
Gran parte della produzione è focalizzata su leghe da pressofusione, anche se non mancano produzioni destinate alla fusione a gravità.
Collaborazioni, più recentemente introdotte, con importanti operatori nel campo dell'alluminio primario (estrusori, laminatori, ecc.), ci hanno permesso di sviluppare un servizio dedicato di trasformazione di scarti, decadenti dalla loro produzione e non più direttamente da essi impiegabili. Usufruendo del nostro know-how e dell'impiantistica disponibile presso i nostri stabilimenti, essi vengono opportunamente rigenerati e restituiti alla funzione originaria, sotto forma di lingotti o sows titolati.
Questa soluzione è particolarmente apprezzata da quelle società che intendono mantenere il controllo del proprio metallo o che cercano di sottrarsi alla volatilità del mercato, assicurandosi una quota di materiale dalle caratteristiche garantite.
In aggiunta all'attività di produzione leghe da fonderia, sopra descritta, vengono mantenuti anche regolari rapporti di fornitura con acciaierie (produzione di pani, nocelle e granelle per disossidazione dell'acciaio, con titoli di alluminio fino al 98%) e con produttori di articoli (polveri, miscele, manicotti, formati, ecc), parimenti progettati per l'impiego siderurgico.
​
La partecipazione attiva da oltre 50 anni alle principali Associazioni nel settore dei metalli non ferrosi ci permette di essere costantemente aggiornati sia sullo sviluppo della tecnologia, che sull'evoluzione a livello nazionale ed europeo delle normative e degli standard ambientali, sempre più stringenti. In più di un'occasione anche clienti o fornitori hanno potuto trarre vantaggio dal confronto coi nostri tecnici su questi temi, che continuano ad assumere ruoli sempre più rilevanti.
​